NATIONAL HARBOR, Md. — On the floor of Sea-Air-Space, the U.S. Navy’s largest annual trade show, Mark Massie pointed to a table with three metal parts.
These were no ordinary metal widgets, argued Massie, who is a program manager for additive manufacturing — another term for 3D printing — at Naval Sea Systems Command. The three parts were built with 3D printers and delivered in less than a year, ready to go on ships.
“Metal additive manufacturing is ready for prime time,” he said.
Earlier this month, the Navy finished a 45-day review of its shipbuilding programs to assess delays caused by the coronavirus pandemic. It found many, including key vessels like aircraft carriers and submarines, were far behind schedule due to a lack of workers and a brittle supply chain.
For both issues, 3D printing could be the answer. To wit, the Navy says work at its Additive Manufacturing Center of Excellence in Virginia is crucial to its plans for building submarines. Sailors on select ships, too, are using the equipment to build parts they need at sea.
Even still, Massie was cautious about the technology.
“We’re definitely still at the interim phase,” he told Defense News.
The needs are perhaps most clear for the Navy, and yet even for that service, the technology — and the path to using it more widely — is still growing. Describing his command’s additive manufacturing strategy, Massie listed three challenges.
The first is getting more companies on contract.
In March 2023, his office issued a statement of need for 3D-printed parts. Using a shortcut procurement tool known as an other transaction authority, eight vendors signed contracts within six months, and then parts — including those on the display table — arrived in about nine months.
Still, the Navy needs to send a clearer signal to companies, Massie noted. Eight vendors is a start, he explained, but it’s not enough.
The second challenge is simplifying the process by which the Pentagon buys 3D-printed materials.
The other transaction authority illustrates two sides to the existing process. On one hand, Massie said, it shows how quickly the Defense Department can move to buy parts. On the other, it shows that the department is still learning how to buy them.
“We’re not quite there yet, but eventually it will look and feel a lot like procuring traditional materials,” he said.
The final issue involves testing the parts once they’re acquired. It’s one thing to design materials in a lab, but anything the Navy would use on a ship must undergo testing in the field. Officials have identified parts considered low risk for such testing, and service members are working to integrate them onto ships.
“Ideally you just go order the parts from supply and it’s approved and it gets right in,” Massie said. “But the reality is it’s not going to be that easy for us.”
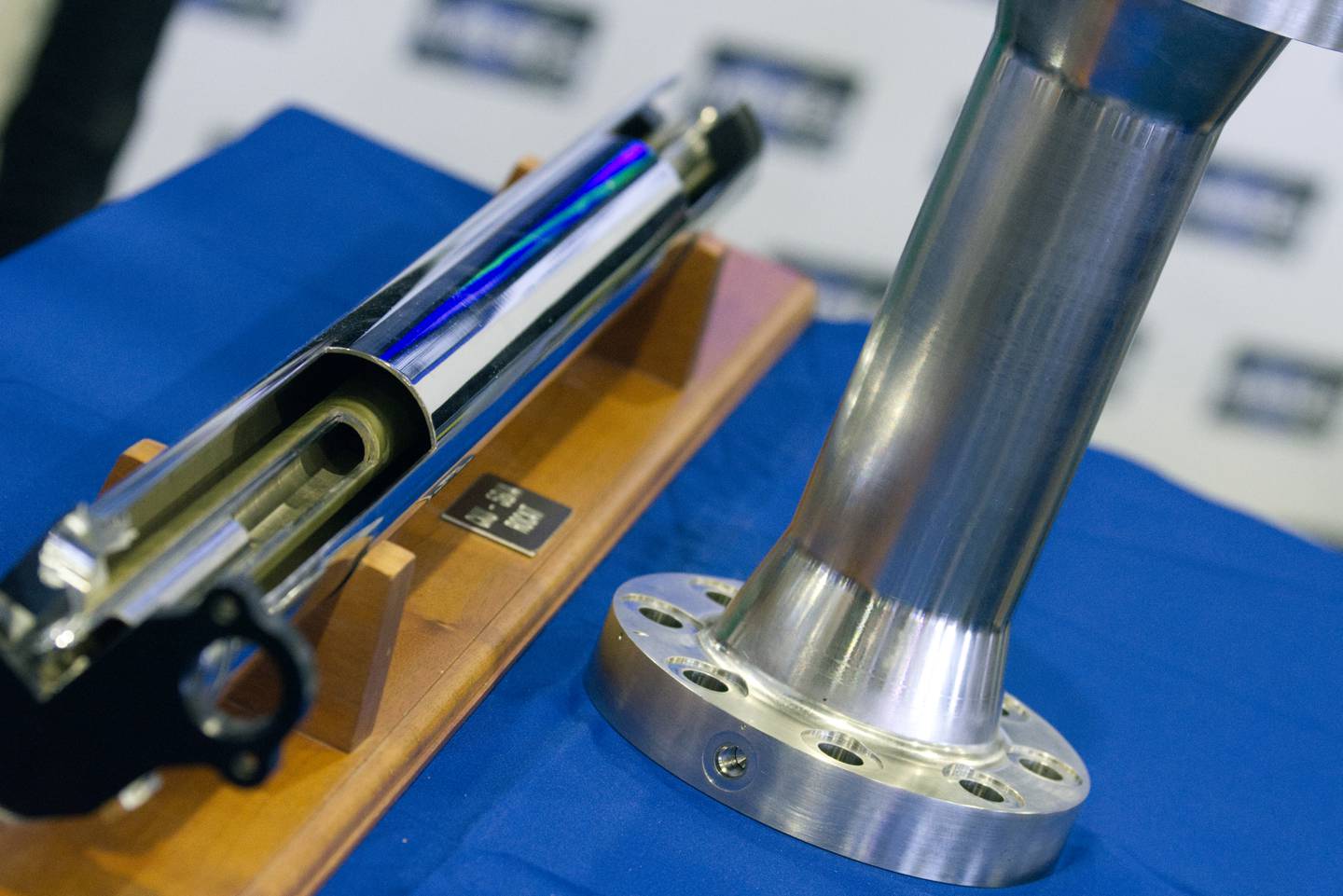
Speaking with reporters last week, Chris Kastner, the chief executive of the shipbuilder HII, described similar challenges.
The biggest role his company will play in 3D printing, Kastner said, won’t be building the parts themselves. Instead, it will be regulatory — getting approval from the Navy to use such parts on ships.
Kastner said he expects those approvals to increase.
“It’s here, it’s happening,” he said of 3D printing. “I would like it to happen much more quickly and [there be] more of it.”
Last May, the Pentagon described in a letter what parts it thinks are safe enough to build with 3D printers and then test on vessels, Massie said.
James Pluta, also a program manager for additive manufacturing at Naval Sea Systems Command, said those approvals are a sign of how comfortable the Defense Department is with the technology.
“Every year or so we’re getting newer guidance ... from leadership that says we don’t just want you to use additive manufacturing, we want you to use it at all opportunities” for these low-risk items, Pluta said.
Speaking on the show floor, he cited examples of ships that needed parts too small to order alone — or below a threshold called the “lowest replaceable unit” — but without which sailors would lose a key capability, such as flying aircraft. In each example, the Navy used 3D printers to rush parts to those sailors, who then fixed the issue.
This year, the Navy plans to focus on installing such materials ashore. But next year, Pluta said, the service has money to install printers on ships, submarines and carriers — around 40 to 50 for polymer parts, and 10 or so for metal ones.
“Over the next year or two,” Pluta said, “we’re going to start to see confidence levels in 3D-printed parts [on ships] increase.”
Noah Robertson is the Pentagon reporter at Defense News. He previously covered national security for the Christian Science Monitor. He holds a bachelor’s degree in English and government from the College of William & Mary in his hometown of Williamsburg, Virginia.
Megan Eckstein is the naval warfare reporter at Defense News. She has covered military news since 2009, with a focus on U.S. Navy and Marine Corps operations, acquisition programs and budgets. She has reported from four geographic fleets and is happiest when she’s filing stories from a ship. Megan is a University of Maryland alumna.